Winding Sticks
As woodworkers we need a way to be sure our materials are straight, flat, and without twist. Machines will usually take care of this, but with hand tools we must find other ways. Traditionally, winding sticks were used to measure the amount of twist in a board. By laying one stick at each end of the board and sighting down them, they will exaggerate the twist so it’s visible. The idea is to measure for twist, plane down the high corners, and re-measure until the sticks are parallel to each other. Below, I will describe how to make this.
TOOLS
Required:
- Hand Plane (#4, #5, Low Angle Jack, etc.)
- Dovetail or Gent Saw
- Marking Knife
- 3/4” Chisel
- Mallet
- Drill and bit
- Clamps or Blue Tape
Optional:
- Panel Saw
- Router Plane
- Bevel Gauge or Dovetail Marker
INSTRUCTIONS
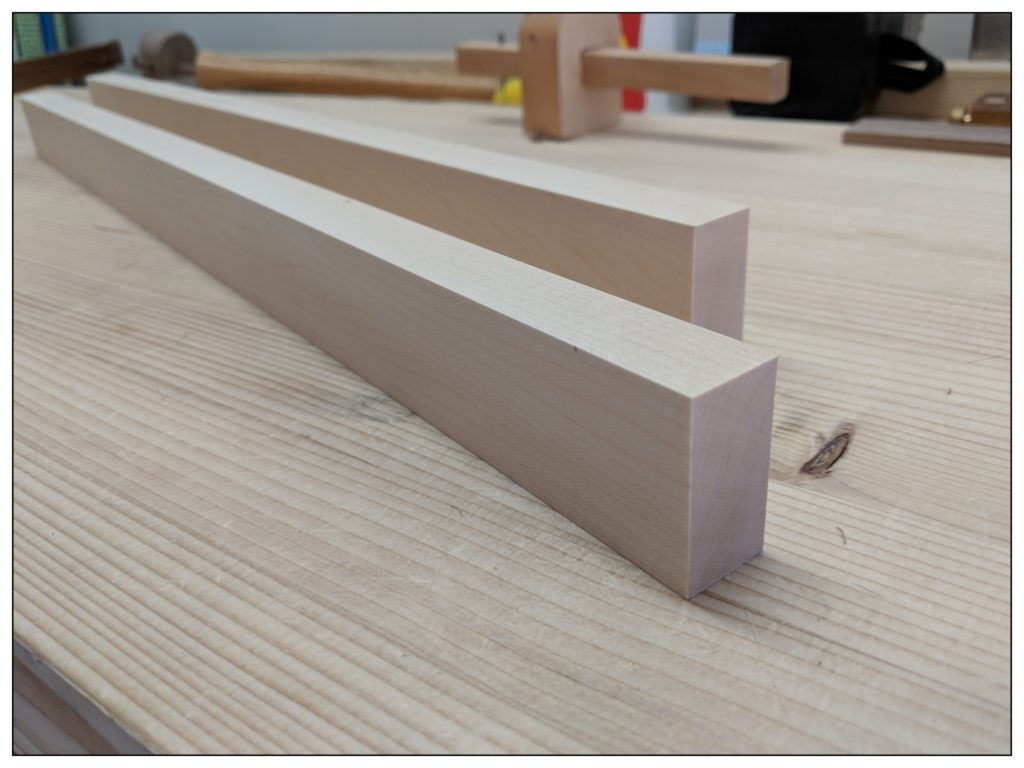
If needed, use the optional panel saw to rip these pieces from larger stock. Otherwise, take any two scrap sticks you might have. I made mine from 3/4″ Maple about 22″ long and about 2 1⁄2” wide. Be sure to plane them nice and straight and that both pieces are parallel.
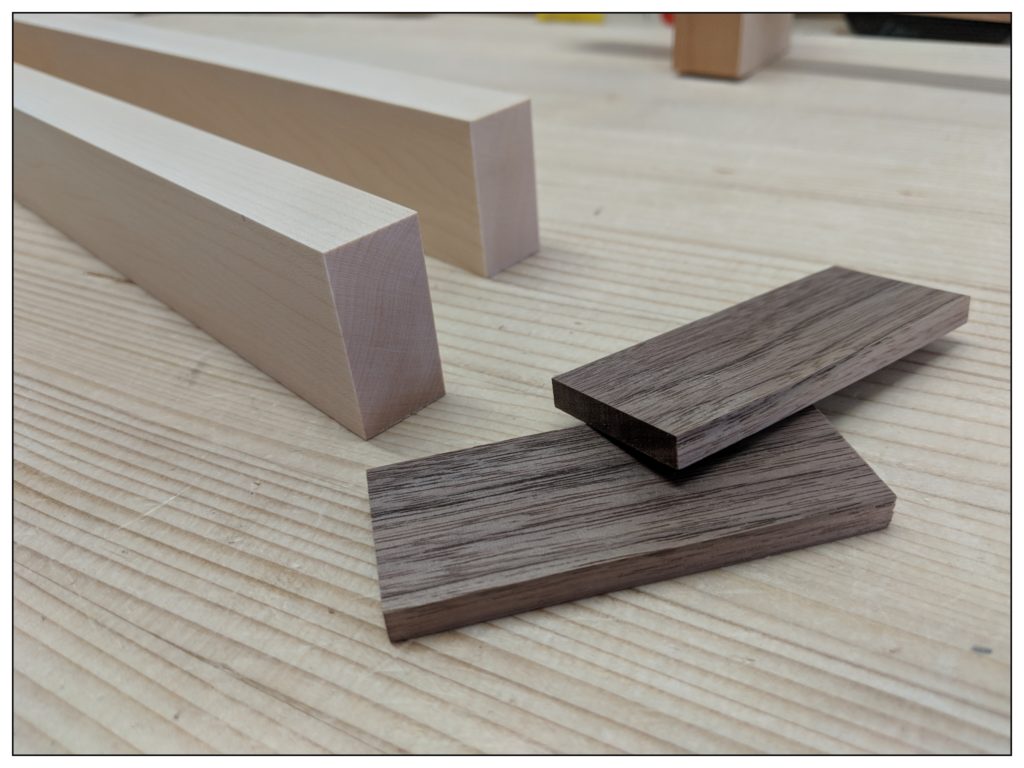
I found two thin scrap pieces of Walnut. Any kind of scrap should work, just be sure it is a contrasting color to the sticks. This will help when you sight down the sticks.
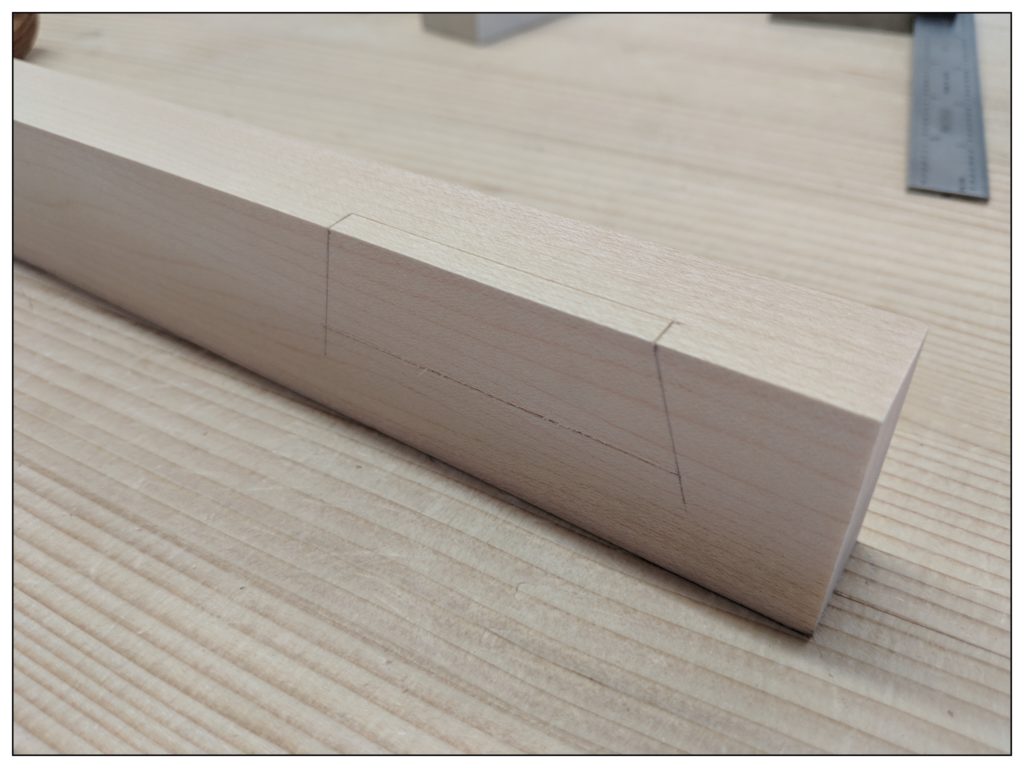
Measure and mark out a small area that the small scraps will sit in. I make mine in the shape of a dovetail. This is purely decorative, you could make them rectangular if you want. Also, the small scraps I have are about 1/4” thick so I mark mine to be 3/16” to allow me to plane the surface flush.
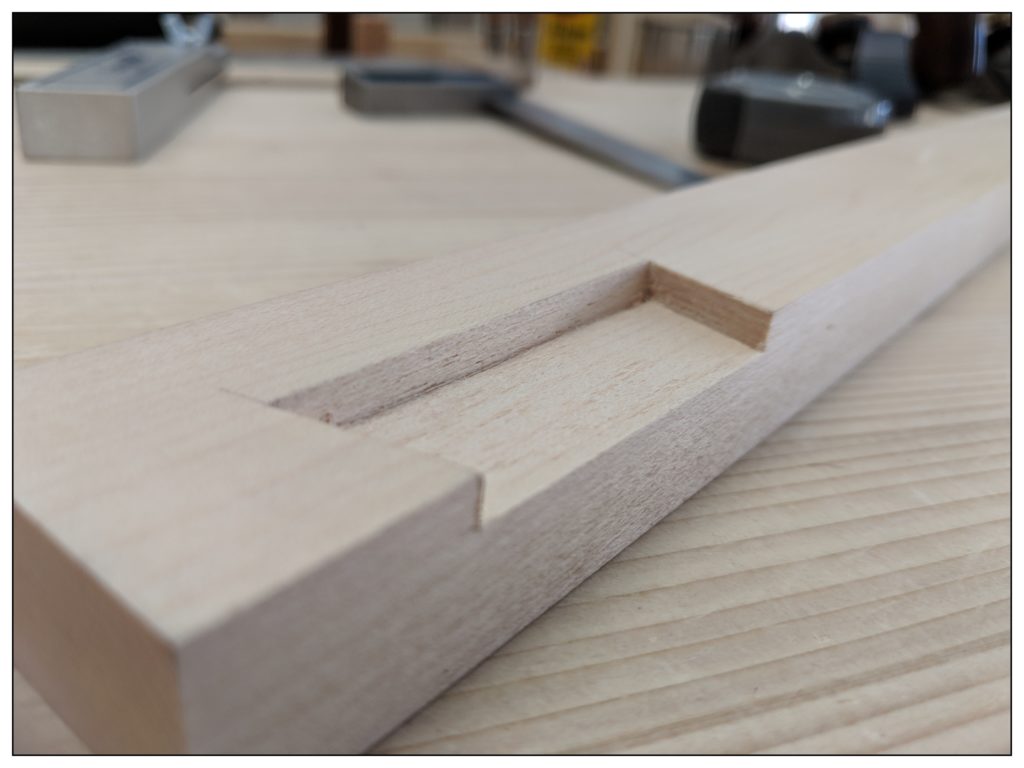
Score lines on your marks with a marking knife. Then take your chisel and carefully start chiseling away the waste using those lines as guides. You can use the optional router plane to clear out the bottom of the housing. Otherwise, just pair carefully with your chisel.
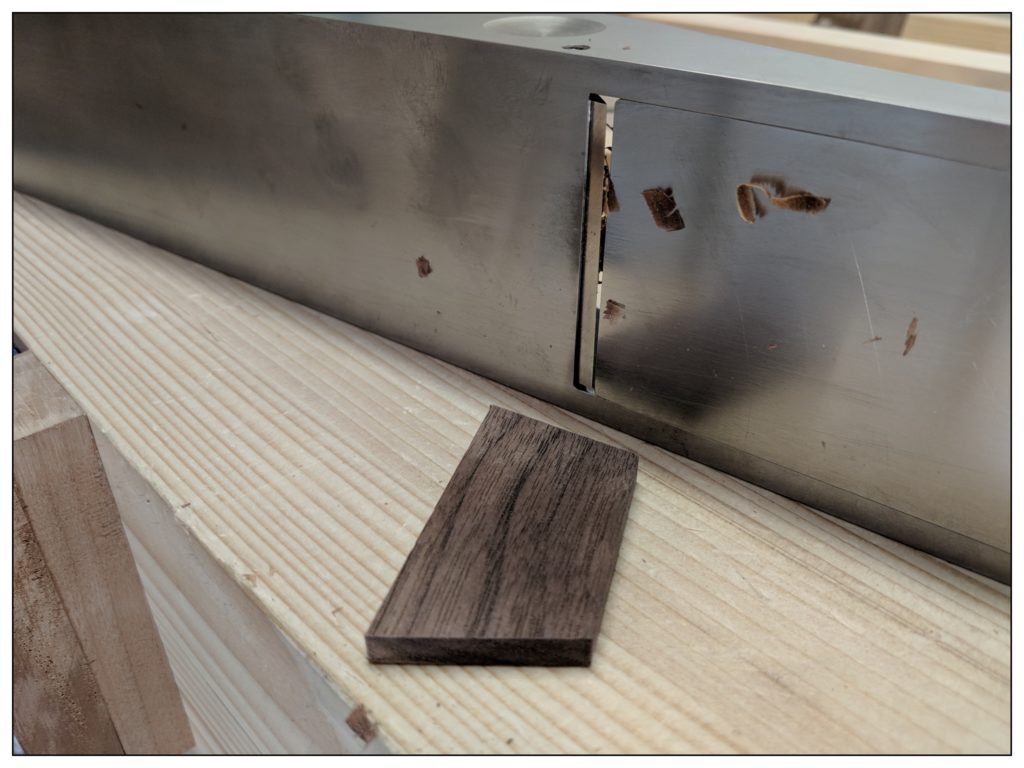
Now, grab the small scraps and line them up with the housing to get the actual size. Make a mark and use a dovetail or gents saw to cut it to size. This piece is too small to try and plane so instead put your plane on its side, grab the piece, and swipe it along the bottom of the plane until the edges are smooth.
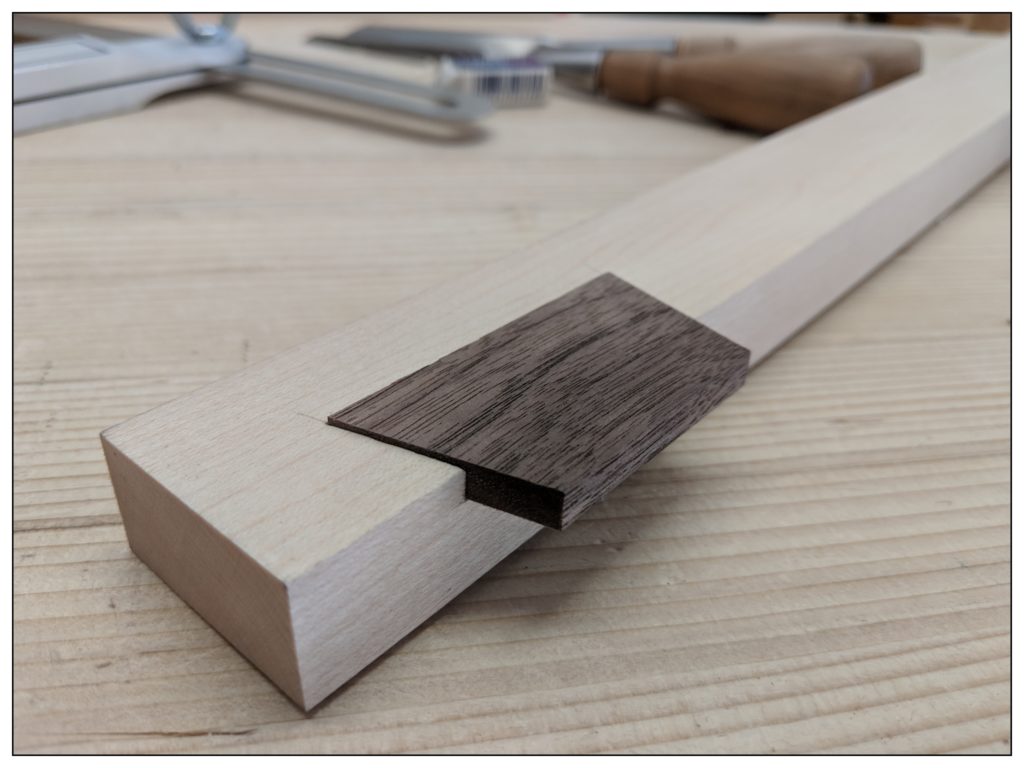
Take a shaving and test fit. Do this repeatedly until it fits snug, but not tight. Notice how it sits proud of the surface. This is so I can cut and plane it down and flush to the surface.
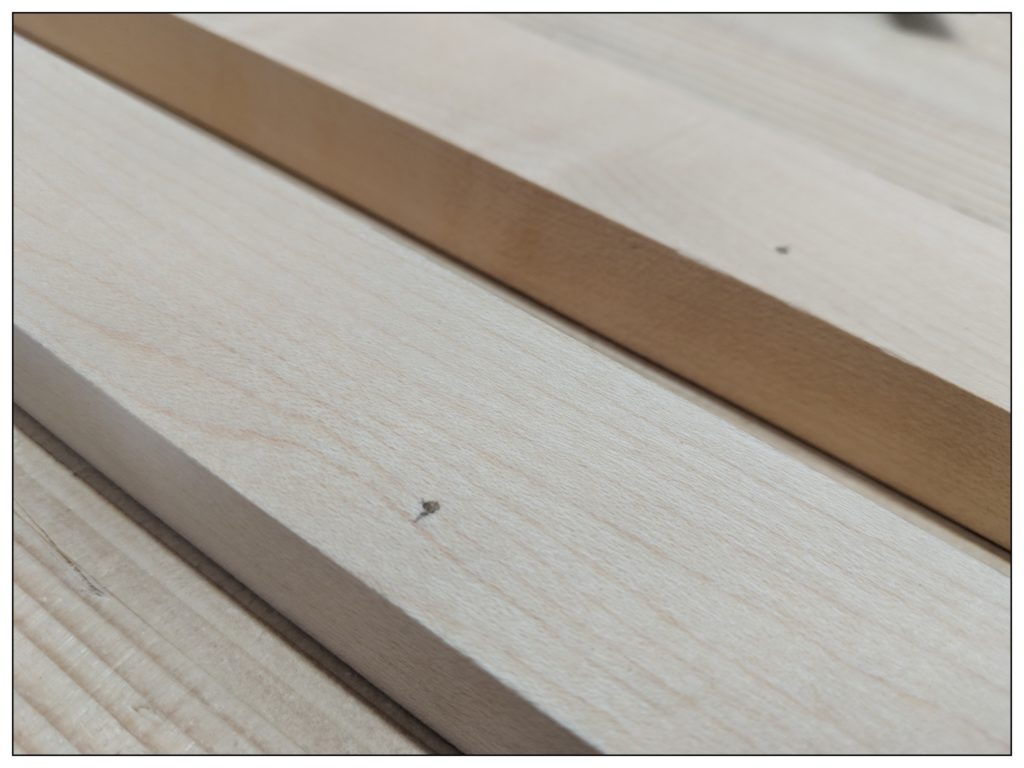
Next step is to mark out the spot for the center markings. These markings are used to center the sticks on the piece you are measuring for twist. It makes the measurement more accurate. Find the center point on each stick and mark it. You can also use an awl or marking knife to create a small hole used to get your drill bit started.
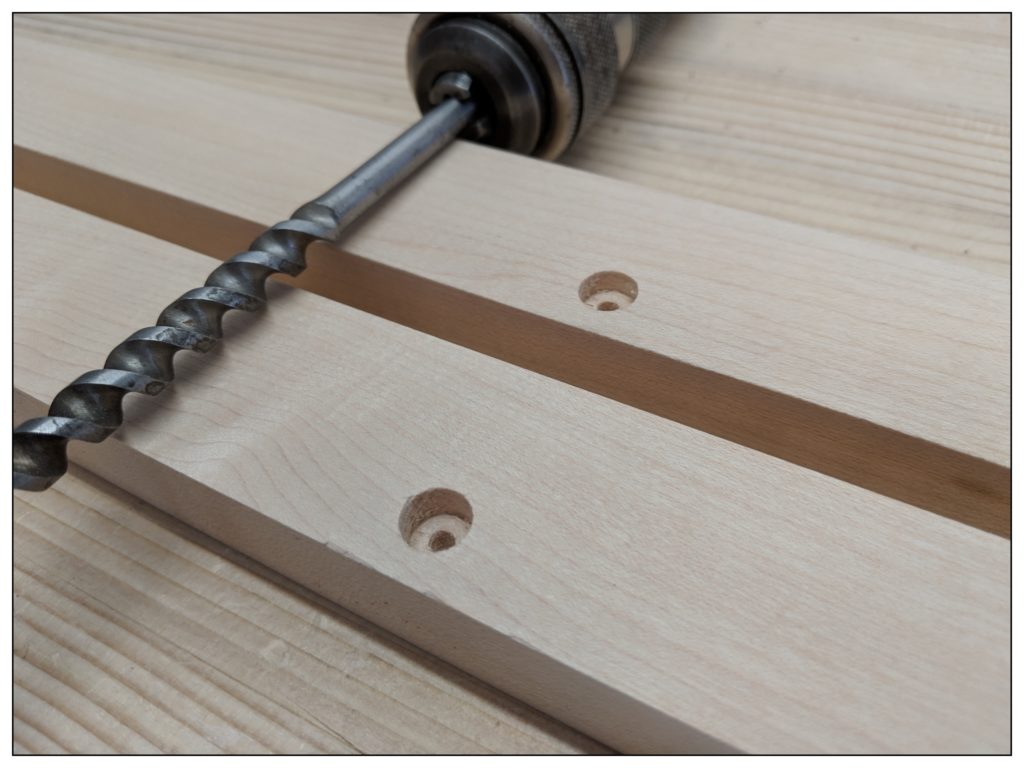
Now, drill down about half way. The diameter of the hole is personal preference, but I made mine about 3/8“.
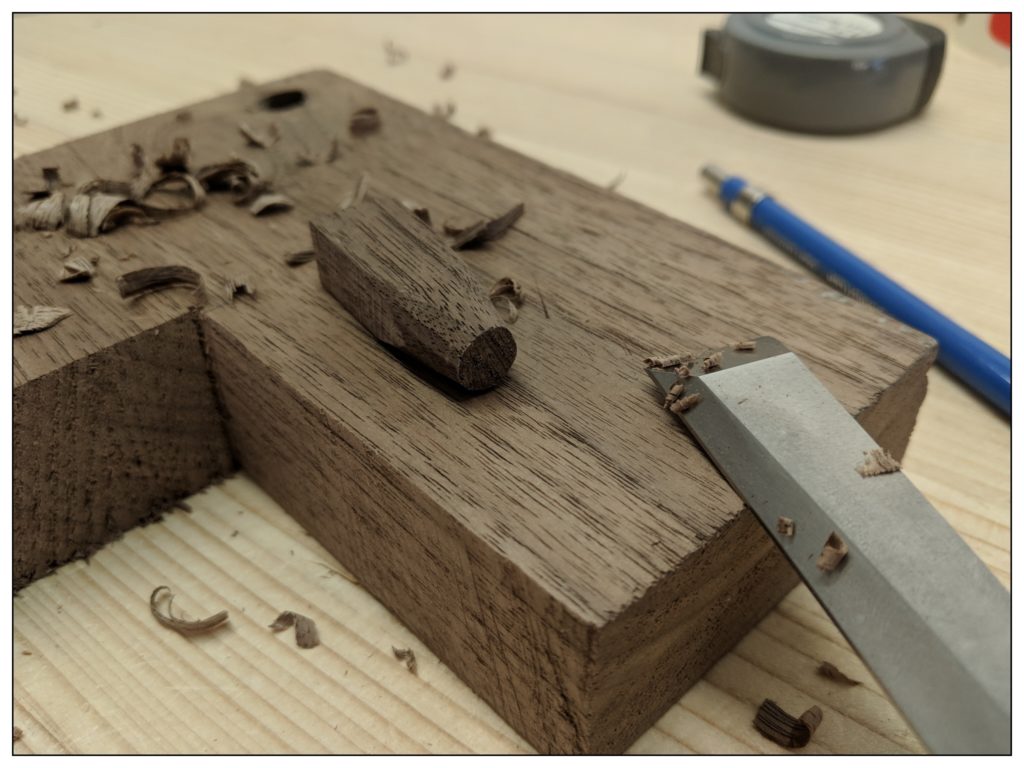
Take a another piece of scrap and use a chisel to pair down the corners until it’s roughly circular. Make sure it is a little smaller than the hole drilled so it will seat properly. Take small cuts and test fit constantly. If it gets too narrow, you can cut off the small end and keep trying.
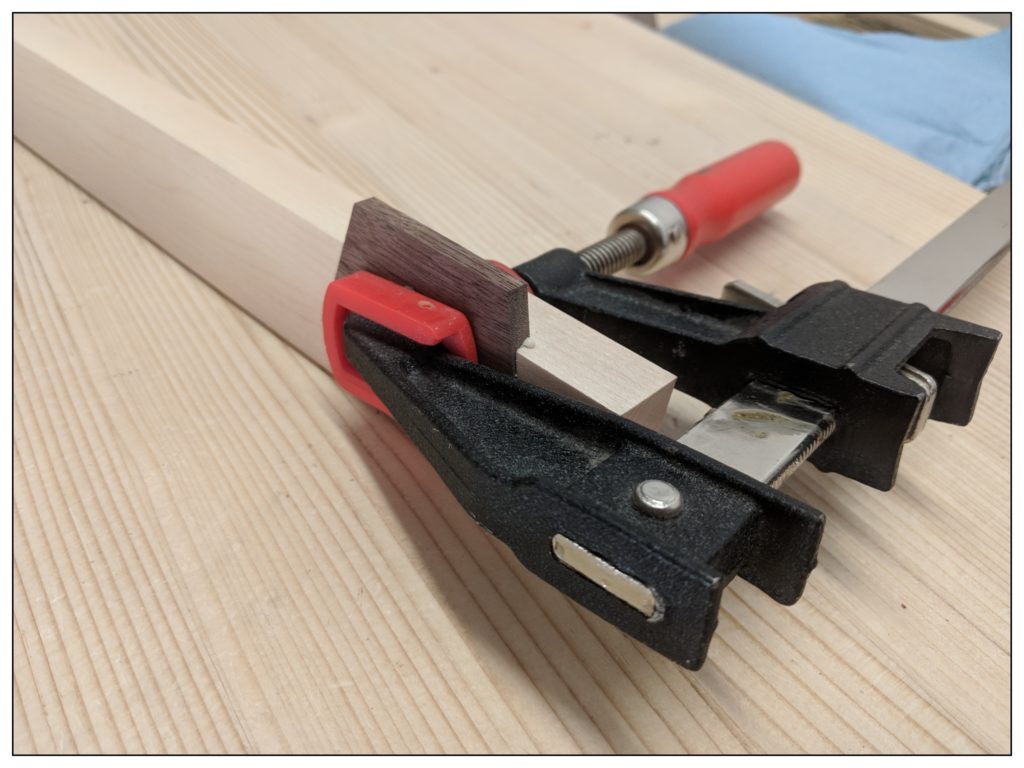
All materials are cut to size and ready to go. Apply glue and assemble. Clamping will help the joint, but if you don’t have actual clamps, you can use blue tape.
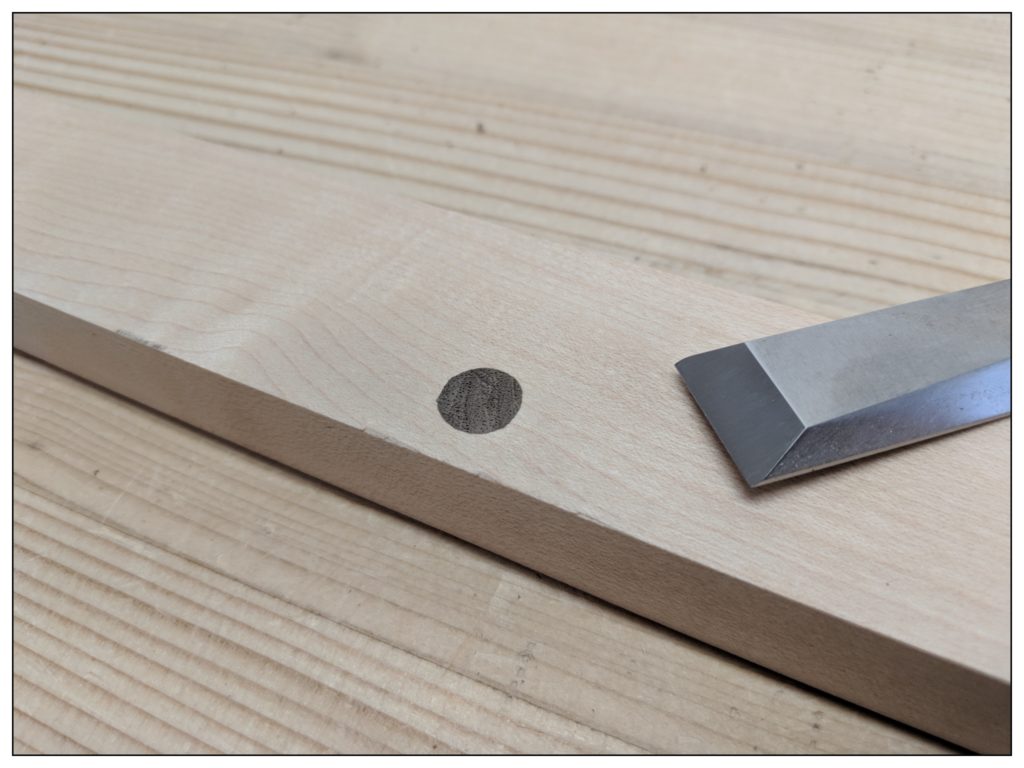
Since none of the glue joints have to resist any forces, 30 minutes to an hour is sufficient for drying. Remove clamps or tape and cut off all protruding pieces. Then using the chisel or hand plane, slowly shave down the remaining material until it’s flush.
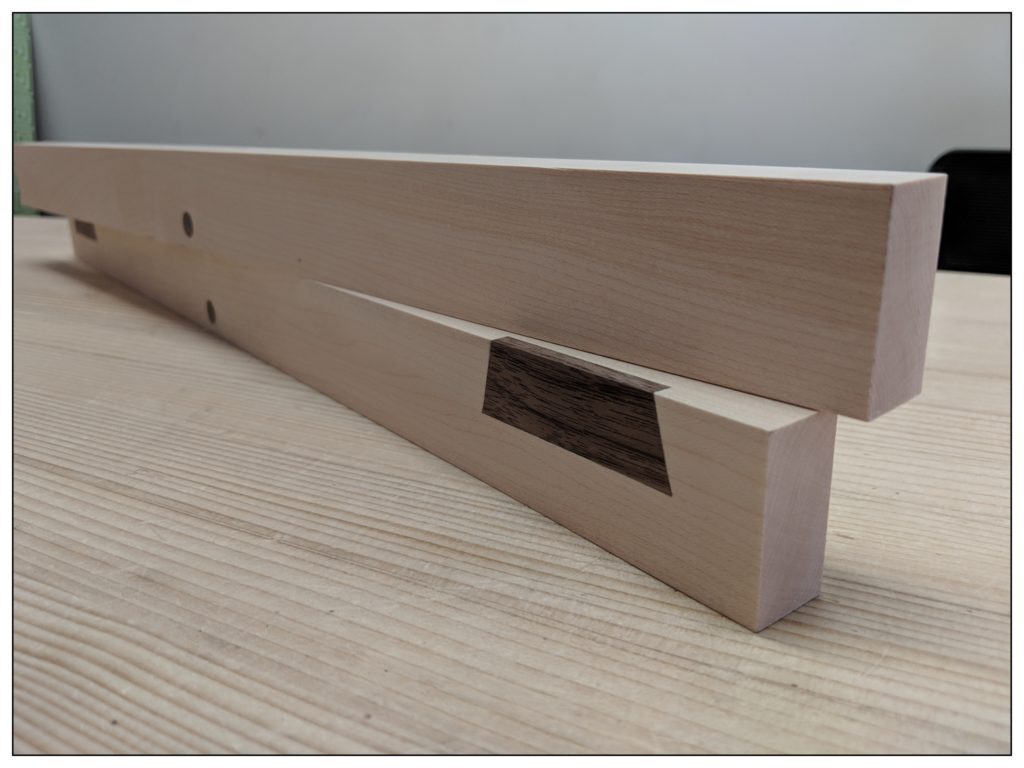
That’s it! You’re done! Just make a final check that the sticks are still straight and parallel. It’s also advisable to take a shaving from all the hard corners so it feels more comfortable in your hands. Finally, while not necessary, you can apply a finish such as Danish oil, Boiled Linseed Oil, or even just paste wax.